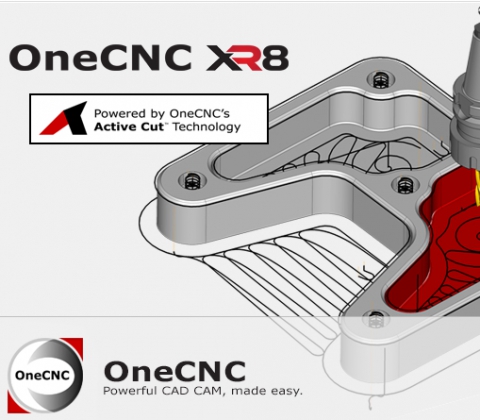
OneCNC XR8 Mill Expert
Published: 20/11/2019We're pleased to announce we've purchased and are currently upgrading all our CAD workstations to OneCNC XR8 Mill Expert.
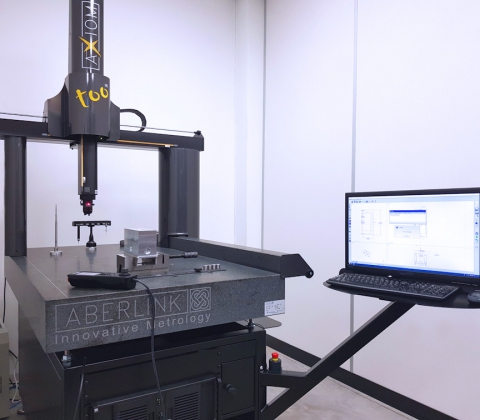
CNC Coordinate Measuring
Published: 15/08/2019We are renowned for the outstanding quality of our components. Commitment to quality is part of our ethos and has set us apart from the competition since the company's establishment in 2001. We are constantly reviewing and improving our machine shop and its processes.
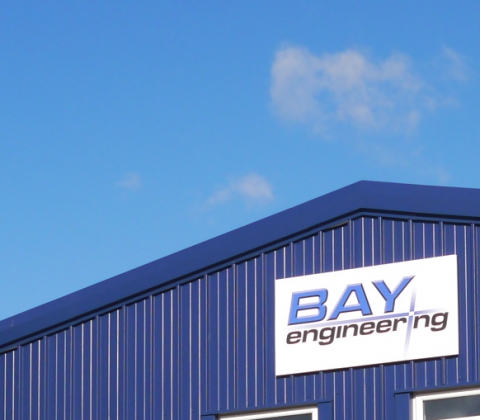
Our future plans
Published: 25/02/2019Bay Engineering is a precision engineering company based in Weymouth, Dorset on the Lynch Lane Industrial Estate. Established in 2001 by Steve Balem and Darren Taylor as a management buyout of ESA Precision Engineering, a company which had been trading for over 25 years.
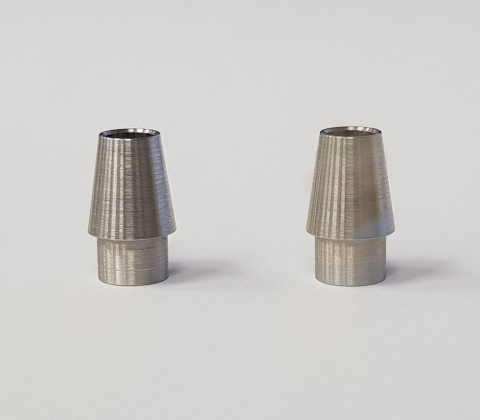
Stainless Steel vs Mild Steel
Published: 15/01/2019When making large batches of components it would be hard to argue that making the part out of steel with zinc plating wouldn’t be cheaper than making it out of stainless steel.
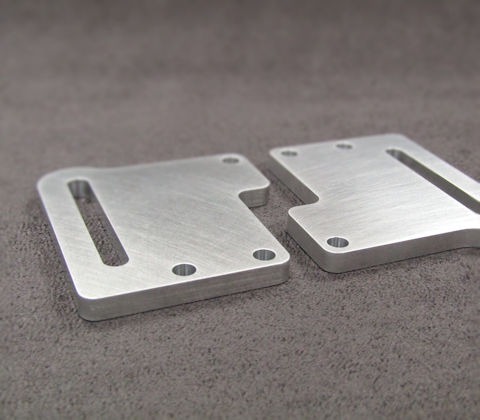
Tooling Plate vs Aluminium
Published: 23/05/2018Aluminium tooling plate has some advantages over normal aluminium plate or bar.
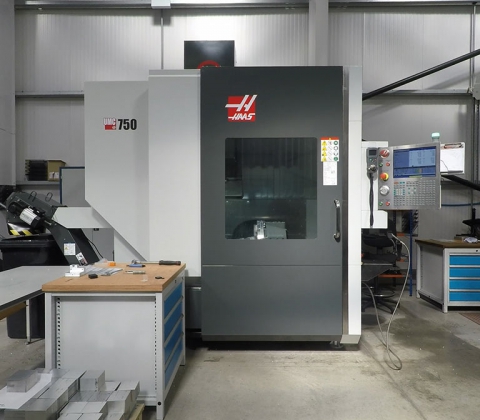
Bay Engineering future-proofs with HAAS (External Article)
Published: 10/07/2017Bay Engineering is a precision engineering company based in Weymouth, Dorset on the Lynch Lane Industrial Estate. They are committed to providing high quality CNC machined components while providing prompt and efficient customer service.
Established in 2001 by directors Steve Balem and Darren Taylor the company has been going from strength to strength.
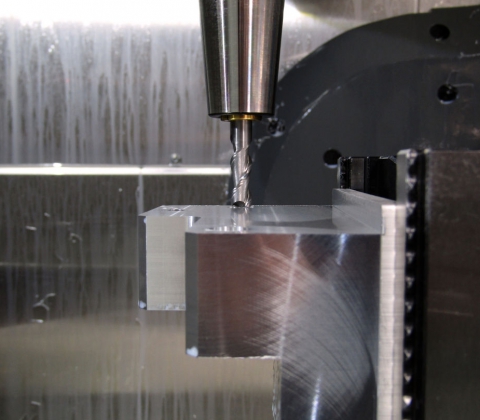
Advantages of 5-axis machining
Published: 12/04/2017As part of our ongoing investment to deliver quality components to our customers, we have purchased another machine capable of 5-axis machining.
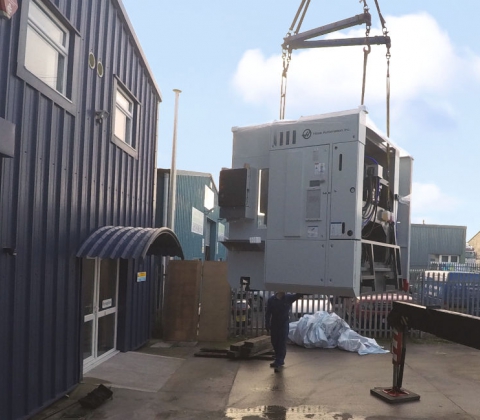
Haas UMC-750 Universal Machining Center
Published: 06/03/2017Bay Engineering is committed to providing the highest quality CNC machined components and customer service to match. To ensure we maintain the highest standards we are renowned for we have just installed our thirteenth machining centre - a Haas UMC-750.
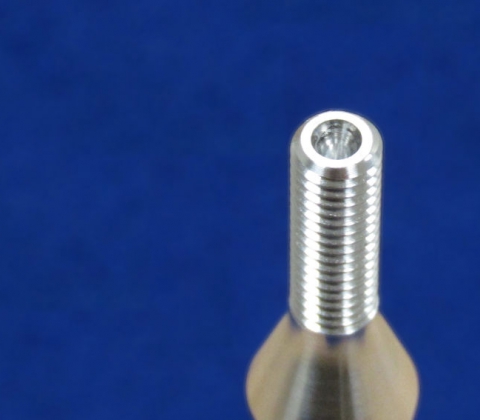
Permitting Centres
Published: 27/02/2017When trying to obtain competitively priced components, a factor to be considered when designing long slender components is whether a centre is acceptable on the finished component.
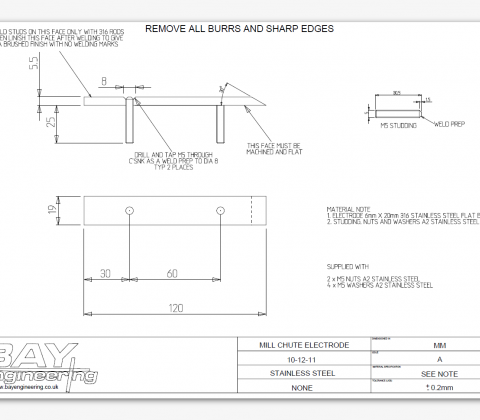
Drawing Formats
Published: 09/01/2017Drawings are quite often sent to us in the PDF format. This normally results in clear, easy to read drawings that we can print out for use in the workshop. This is a very effective means of sending drawings.
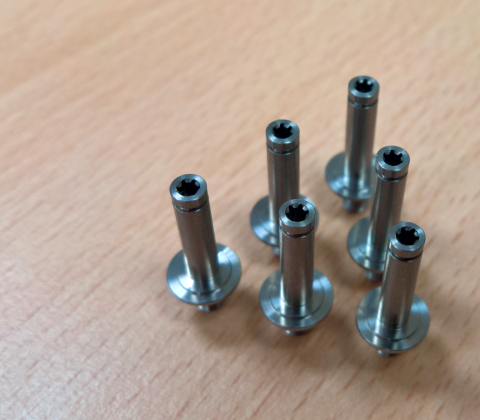
Broaching for Allen/hex keys, Torx etc.
Published: 30/11/2016We are now able to offer you the facility to produce internal hexagons to suit your requirements, with the recent addition of a new broaching tool. Internal hexagonal forms can be produced in house, commonly to suit Allen or hex keys, but other forms are available on request e.g. Torx, spline or square forms etc.
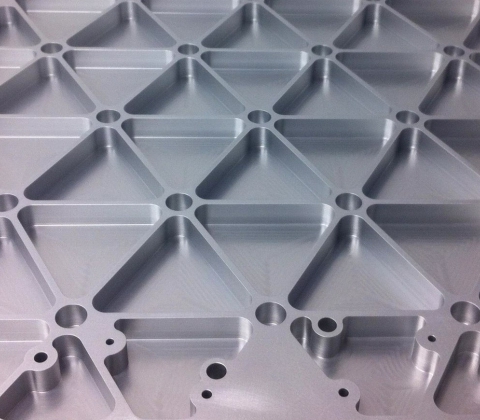
Cutting Corners
Published: 28/10/2016When machining an internal corner radius on a CNC milling machine it is normally an advantage to use as large a cutter as possible. Therefore, if a component has an internal radius of 6mm the ideal cutter to use would be 12mm diameter (6mm radius). Unfortunately, when a cutter and internal radius are the same size chatter can occur due to the fact that for the brief moment the cutter is in the corner it has a lot of surface contact. This may mean that a 10mm cutter is chosen as a compromise.
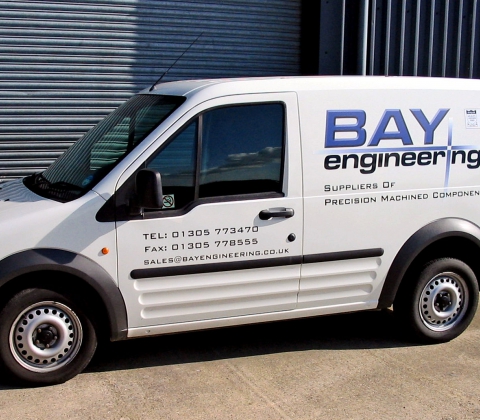
Our Lead Times
Published: 12/10/2016We are often asked about our lead times. As a standard we try to offer 4 weeks. We will accommodate shorter lead times whenever possible if it is required and we can achieve the date requested without impacting on our existing commitments. Please ask if you require a quick turnaround.
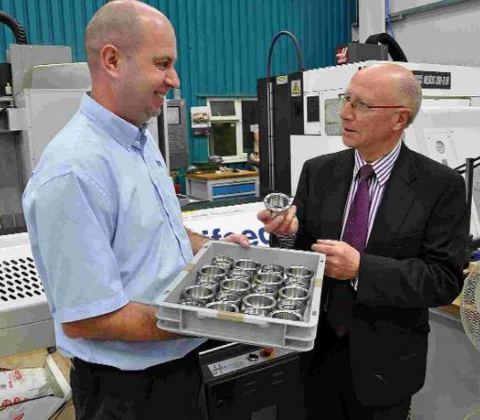
£1m turnover for Weymouth engineers' firm (External Article)
Published: 20/11/2013A WEYMOUTH-BASED engineering firm is set to double its turnover to £1million after it was paired with a specialist mentor.